How to Recover and Recycle UPS Batteries
The primary energy storage component within an uninterruptible power supply is its battery set. Whether this is short runtime battery providing less than 5 minutes runtime or a larger battery set covering several hours of backup, the battery set would be based on a lead acid battery. During the last couple of years lithium-ion battery technologies have advanced rapidly, driven by their demand within the electric vehicle industry and for grid-scale energy storage.
Today the traditional valve regulated lead acid (VRLA) UPS battery faces stiff competition from lithium-ion competitors. The reasons for this are several and are mainly due-to-the-fact that lithium-ion (Li-ion) batteries are less temperature sensitive, with a higher power density and are capable of almost unlimited charge and rapid recharge cycles. As lithium battery production has ramped up to meet rising demand, so the prices per battery block has reduced. We are a long way from parity with lead acid UPS batteries but within the next 5 years the price gap will close rapidly.
Recycling Lead Acid UPS Batteries
Most batteries will last to within 70-90% of their design life before they require replacement. The typical VRLA batteries used within UPS installations are either 5-year or 10-year design life products which will require replacement around years 3-4 and 7-8. This is dependent upon the ambient temperature they are operated within, which should be 20-25˚C, the number of charge/discharge cycles they are run for and other factors including their design and production quality and the sophistication of their UPS battery charging circuit. Lithium-ion batteries have a design life of 10 years or more.
VRLA batteries tend to have plastic case and this may or not be made from non-flammable materials to BS 6290 part 4. Batteries approaching their end of life can be discovered via visual inspection, UPS battery monitoring systems and individual battery block testing.
Lead acid batteries are exothermic and give off heat during their charging. During discharge they are endothermic and absorb heat. The heating effect builds due to the chemical reaction between the hydrochloric acid electrolyte and lead plates. The electrolyte tends to be a gel rather than a liquid in a VRLA battery. Glass cased batteries typically have a liquid electrolyte. Over time the heat can lead to the plastic case buckling and even cracking. There can also be white deposits of the electrolyte around the battery terminals.
When a battery has reached this state it is beyond its end of life and is a potential risk to the UPS installation in form of thermal runaway. A battery set is also only as strong as its weakest battery block as a weakened battery will lower the overall performance over time of a battery string.
Therefore, batteries should be replaced before they reach this state of physical deterioration. UPS battery monitoring systems and annual battery block testing can help to identify failing batteries and the best time to plan for a battery replacement.
Whether the lead acid UPS battery is in tact or has a buckled or cracked case, it must be treated as hazardous waste and to national regulations. In the UK, UPS battery recycling is heavily regulated under the Waste Electrical and Electronic Equipment recycling (WEEE) directive.
Contractors who transport such waste must be registered with the Environment Agency and for health & safety reasons, they must be trained to suitable standards including working within AC and DC power environments, handling batteries and hazardous substances. Batteries removed from site must be taken to a registered recycling centre and waste transfer notes provided for traceability.
Lead acid batteries are regularly recycled and up to 90% of the material can be reclaimed for later usage. The plastic cases, which tend to be made from polypropylene can be recycled into new battery cases. The lead plates can be smelted down and used within new batteries. Even the sulphuric acid electrolyte can be reclaimed and sold on for other uses.
Recovering Lithium UPS Batteries
Despite their on-site benefits to a UPS or energy storage installation, transporting lithium batteries and recycling them presents more issues than lead acid batteries. The transportation of lithium-ion batteries is prohibited in some instances when they are no within the products they are used with. This is because they can pose a fire risk when damaged or exposed to water which can lead to the forming of lithium hydroxide and hydrogen gas. For this reasons airline transportation by UK airline is banned.
Unlike lead acid battery recycling, lithium-ion battery recycling in the UK is extremely difficult as there are no recycling facilities. The nearest being in Belgium (more information: https://resource.co/article/ion-prize-how-recycle-lithium-batteries-12630). This places greater need on safe transportation and rising costs for removal and their eventual recycling. The costs of the recycled lithium are also high and by as much as five times compared to new material.
Summary
When looking at the Total Cost of Ownership (TCO) of a UPS system it is important to cover the complete life-cycle costs from installation to eventual end-of-life disposal. Lithium-ion batteries offer several advantages for serve room and datacentre applications but have a higher purchase price than VRLA batteries and higher end-of-life disposal costs. These costs will fall over time and care should be taken when considering which UPS battery type to install for new systems within the next few years. There are established process for the recovering and recycling of lead acid batteries within UPS systems and it is therefore important to work with an established and certified UPS and battery recycling company.
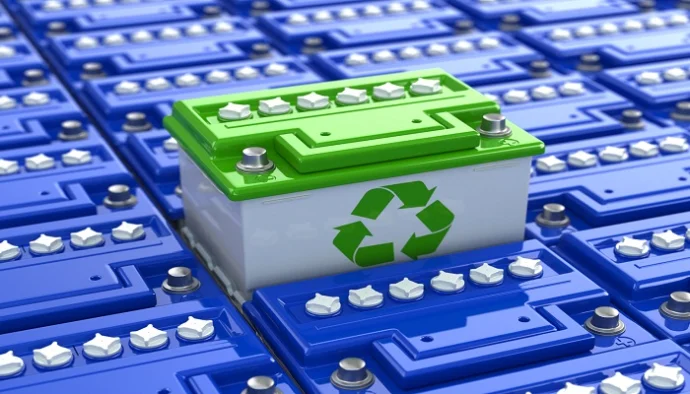