Removing, Relocating or Recycling Server Room Systems
When considering a major server room or data centre refresh, it is important to consider the effect on existing infrastructure systems including: server rack cabinets, uninterruptible power supplies and air conditioning units. These are complex systems whose removal requires consideration of many factors including downtime, risk assessment and methods, logistics, decommissioning and environmental impacts.
Planned and Emergency System Downtime
There are two types of system downtime: Planned and Unplanned:
- Planned infers that the site or part of it has been powered own allowing for a server rack or UPS system or cooling system to be completely powered down and isolated for removal. With sound project management, time will have been spent planning this move, with a critical path analysis and risk assessment and method statement that covers all the aspects of the project.
- Emergency or unplanned downtime is when the on-site team must provide a far faster server and short response time. Often this is due to failure of an individual system within the datacentre environment or one that has failed a preventative maintenance inspection. Examples of this could include a UPS system failure or the need to replace batteries within the uninterruptible power supply. An air conditioning unit or part of the system could have failed, or a critical component or consumable require replacement.
Whether the downtime is planned or an emergency event, the procedure of removal and/or replacement will often follow the same process, just with shorter time frames. Whatever the pace of the replacement, health and safety, and sound practice should be observed always.
The date and time the service required is also important as it can directly affect cost and availability of engineers and resources. Typical working hours are Monday to Friday 8:30 to 17:00pm. Outside working hours incur higher costs and more so for weekend and bank holiday times.
Server Room Equipment Removal Checklist
Removing an IT system or part of the critical infrastructure is almost always an inverse of the installation and commissioning process. The first stage is the review the entire installation and the following checklist covers the principle areas that should be considered.
Site Surveys
When asked to assist, advice or carry out an IT equipment removal project we will ask for several pieces of information to assess the complexity of the project. The basic information we require includes:
- Equipment age, manufacturer or brand, physical condition and model numbers
- Photographs of the equipment, the environment and route to be taken
- Site considerations including access, security, restrictions and permits
- Location including a full address and postcode
- Project timescales
Not all this information may be available but the more that is available the easiest it will be for us to assess the project. If a site survey or ‘deep dive’ into the project is required, this will cover further areas including:
Logistics Planning For Removals and Relocations
It may have been several years since the server room or datacentre was built. The installation could have changed over that time and there no longer be as easy access as there was. The first step therefore is to review how easy it will be to move the in-situ equipment from its current location to its new location. The new location could be to outside the building for collection or to another location within the facility. Factors to consider include:
- Raise access floors, plinths, steps and door frames. Just how easy will it be to move the server rack, UPS or CRAC unit outside of its current room? Specialist logistics equipment can include cranes, hoists, trolleys and stair climbers. Door frame widths should also be considered.
- What is the route from the equipment location to the new location or collection point. Specialist logistics equipment may again be required. If a lift can be used, the weight loading will need to be checked. If there are floors with specialist finishes they may need protecting. If the equipment must be taken to a loading ramp what off-loading facilities (forklifts) are available and what type of collection vehicle will be required (tail-lift or side curtain).
- Often an overlooked area but the original packing is rarely kept on site and stored for any length of time. When moving equipment from site it is often easiest to put this onto a pallet and to shrink-wrapped. Card board outers may be used for additional protection. Specialist cases with moulded foam inners may be required for sensitive IT network components including servers and routers.
- If there is a chance of the equipment leaking, then the appropriate plastic containers may be required. Air conditioning units can contain water collected as part of their dehumidification and this could be contaminated if left untreated. Lead acid batteries can use a gel or more liquid electrolyte which can leak from cracked cases.
Logistics is by far the main consideration when removing equipment from site due to the size and weight of the equipment to be removed. Server racks when fully loaded can be several hundred kilograms in weight. UPS batteries being lead-based are heavy and anything above 20Kg will require a two-person lift or specialist moving equipment.
Datacentre Hardware Disconnection and Decommissioning
Any system connected to the server room or datacentre infrastructure will require safe disconnection for transportation. This aspect of the project may include electrical connections, both AC mains power and DC power (battery packs), network connections and ducting.
- Temporary supplies. Will the site require temporary power or cooling during the removal and replacement project? UPS systems, generators and air conditioners can be provided on a short-term rental basis to provide power protection and cooling for a site.
- Electrical Contractors: Will the site work require the work to be undertaken by a certified NICEIC or ECA electrical contractor? Does the work require specific battery knowledge and certification, noting that all electrical contractors can provide Direct Current (DC) certified engineers.
- Specialist Certified Engineers. Will the project require manufacturer trained engineer including certified UPS service engineers or certified Air Conditioning service engineers?
- Rectification works. If the equipment is not to be replaced are works required to main the resilience of the environment and its energy efficiency? Removal of equipment can leave spaces within server racks, floors and even ceilings that can lead to lower operating efficiencies for cooling systems. Rack blanking plates, replacement floor and ceiling tiles may be required as may general dilapidation services including painting and decorating of walls and especially where wall-mounted or close-to-wall equipment has been removed or moved.
Once the equipment has been disconnected and decommissioned it should then be in a safe condition for removal. Where equipment is to be moved and rebuilt on another site we recommend that a drawing and photographs are made of the system and its connections prior to disconnection. Consider a complex server rack that can include servers, IT peripherals, network and power cable connections, remote monitoring interfaces, rear door cooling, in-rack cooling, UPS systems and PDUs. This is a complex cabinet and the drawing and photographs provide an historical record of the operative connections and condition which could assist the rebuild.
IT System Recycling and Environmental Considerations
If the removed equipment is to be removed for disposal there are several aspects to consider:
- Waste Carriers License. Certain products are classed as hazardous waste and the company transporting them require a license known as a Waste Carriers License from the Environment Agency (https://www.gov.uk/government/organisations/environment-agency). Lead acid batteries used with UPS systems fall into this category.
- Disposal Centre. The removed equipment will fall under the WEEE and RoHS directives and will require strip-down and disposal via a licensed waste centre. WEE and RoHS are European waste directives applying here to electronic and electrical system disposal and intend to ensure systems are recycled in accordance with regulations, with manufacturers taking responsibility as required for their materials.
- A licensed waste centre may be able to offer a financial rebate for the metals and other materials that can be recovered from the system. The two metals with the highest monetary value include lead (batteries) and copper (cabling). Often the monetary value is based on weight and a weigh bridge is used for large items. The vehicle with the equipment drives onto the weigh bridge and is weighed. The equipment is then off-loaded, and the vehicle weighed again to determine the weight of the systems removed and a monetary value attributed. The payment is often in the form of a cheque or bank transfer for recoding purposes and may be offered back to the original client as a discount or credit from the final bill.
- Documentation: A waste transfer note is a record of the collection and disposal of the equipment from site by the removals and recycling company or companies. This is an important environmental record of the asset disposal which should be retained and available for inspection by auditors and agencies as required.
Sometimes recovered equipment can be made available for rental or resale. Often this is dependent upon its age, condition and refurbishment costs. Where this is not always possible, the recovered system may be kept for spares and this can help for companies looking to maintain and/or repair systems that are no longer in manufacturer. Some older UPS systems and air conditioners can fall into this category.
Life cycle management is an important consideration for all IT, server room or datacentre managers. Equipment will age in use and technology refreshes will always be required to help organisations maintain their competitive advantages and optimum service levels. As well as planned system upgrades and removals, the Server Room Environments team can assist with emergency equipment swap-outs and upgrades, often at short notice.
Download the Server Room Environments checklist for a relocating, removing and/or recycling hardware systems including server cabinets, UPS systems and air conditioning units.
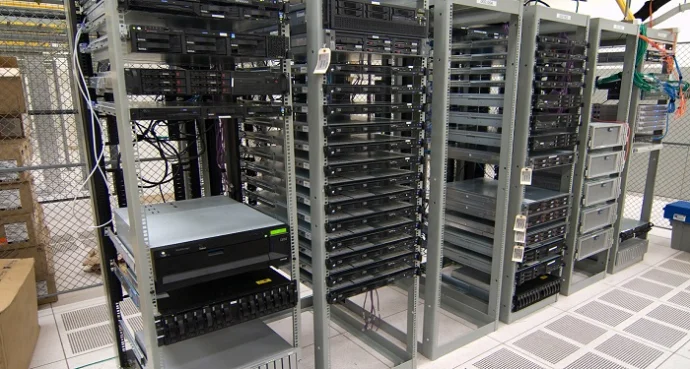